BLOG
Empowering Predictive Maintenance With IoT Remote Monitoring
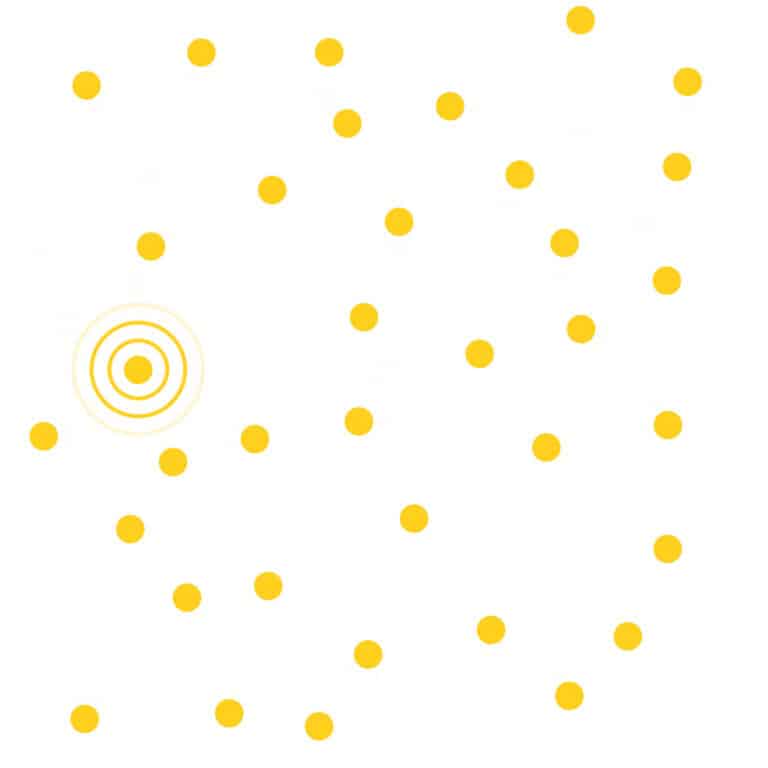
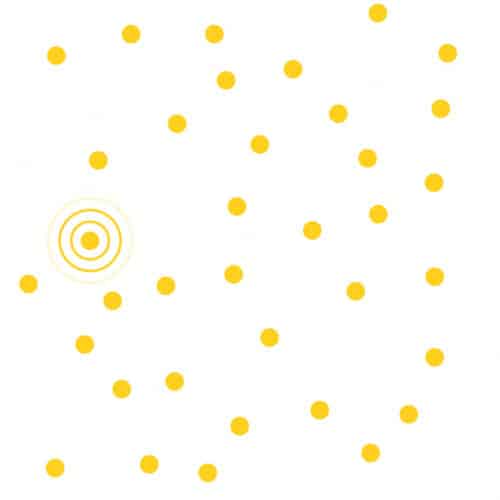
If the existence of fortune tellers and crystal balls can attest to anything, it’s that humans have long attempted to predict what the future holds. But while the efficacy of “supernatural” fortune-telling capabilities may be questionable at best, we have developed a more reliable way to predict the future by way of IoT-enabled predictive maintenance.
Predictive maintenance refers to a technique that employs IoT remote monitoring tools to assess the performance and condition of an asset. In manufacturing, predictive maintenance provides a 10x return on investment on average by increasing throughput, reducing maintenance costs, and minimizing process breakdowns. Machine learning models process data collected from IoT-enabled sensors to predict when equipment is likely to fail, providing an opportunity to prevent the failure entirely. Should equipment fail nonetheless, predictive maintenance can recommend corrective actions to prevent similar failures from occurring in the future.
All of these predictive maintenance capabilities are made possible thanks to IoT remote monitoring technology. In this blog post, we’ll provide an in-depth look at how IoT remote monitoring works, then share three key success strategies for deploying effective predictive maintenance.
First, let’s take a look at what we mean by IoT remote monitoring.
IoT Remote Monitoring: Defined
In the context of manufacturing predictive maintenance, IoT remote monitoring automates the assessment of equipment health and the creation of service requests. Without IoT remote monitoring, plants must rely on staff to manually collect, process, and analyze machine data before issuing actionable next steps for diagnostics or maintenance. IoT remote monitoring technology speeds up the process, leading to lower long-term costs and increased productivity to boot.
How Does Remote Monitoring Work?
Remote monitoring integrates IoT devices and artificial intelligence to gather and analyze machine performance data. IoT devices transmit data describing machine operation and productivity to an AI-enabled platform. That platform analyzes the information and provides personnel with real-time access to machine health insights. Detailed reports with historical performance data also offer snapshots of productivity levels and help inform staff of maintenance schedules.
By leveraging quality historic data, machine learning systems can predict when a breakdown is likely to occur and recommend proactive measures to minimize downtime and optimize maintenance resources.
The Impact of IoT Remote Monitoring on Predictive Maintenance
In the days before remote monitoring, failing machines simply sounded an alarm to alert staff of an issue. Factory floor managers would be dispatched to confirm the problem, technicians called to diagnose and troubleshoot, parts ordered, and repairs scheduled. In the meantime, the manufacturing team would need to think on their feet and work around the loss in productivity.
Today, IoT remote monitoring provides the power to substantially mitigate the issue of unpredicted downtime. Benefits of IoT remote monitoring in predictive maintenance include:
- Scaling data collection
- Reducing long-term costs
- Maximizing machine uptime
- Streamlining the notification process
- Reducing service calls
Leveraging Key Success Strategies for Better Predictive Maintenance With IoT Remote Monitoring
At Very, we leverage three key strategies to help our partners establish effective predictive maintenance empowered by IoT remote monitoring.
- Involve data scientists early on to wrangle the data.
- Automate the data engineering process strategically.
- Present usable output to the right people.
Involve Data Scientists Early On To Wrangle the Data
While some aspects of predictive maintenance and IoT remote monitoring can be addressed by data engineers, data scientists should be involved to ideate and employ your predictive maintenance strategies. Consider that sensor noise, missing data, and other imperfections in your data set may quickly make your analysis efforts feel like you’re trying to herd cats. Data scientists will make the process a lot less painful for you.
First, data scientists will work with your data engineering team to plan for the data pipeline and architecture. Machine learning algorithm outcomes and successful predictive maintenance are only possible with large volumes of clean data. Data scientists will be able to pinpoint any gaps in necessary data volume and help you identify where you’ll need to install new sensors for more data generation.
Second, data scientists help you clean, structure, and label the data. Raw data is rarely the best diet for machine learning algorithms. In addition to duplicates and missing data, incorrect data types may throw errors into downstream processing. Data scientists can identify and remedy data abnormalities as well as isolate the signal of interest from instrumental and environmental noise.
Third, data scientists create and implement effective machine learning models. Predicting equipment failure based on millions of data points is generally impossible using traditional analytical methods. Manufacturers often rely on machine learning to synthesize these vast amounts of data and then output results that translate to maintenance actions. A team of data scientists is responsible for wielding the most effective machine learning tools and passing that expertise to data engineers. (In some cases, you might be able to find a data science team with data engineering capabilities, like Very’s.)
But let’s not forget to mention one crucial caveat: data scientists won’t be able to do the work if they’re left with roadblocks in their path. Prioritize providing your data scientists with the information and tools they’ll need to do the job right. They’ll need technical access (e.g. correct tooling, permissions, servers, etc.), information access, and people access (connections with gatekeepers and conversations with internal domain experts).
Automate the Data Engineering Process Strategically
In the context of predictive maintenance, data engineering is the process of collecting and moving data from machine sensors into a repository, usually in the cloud. From there, it continues through the data pipeline to be cleansed and ingested by machine learning models.
Effective data engineering is reliable, repeatable, and scalable. These characteristics also make the data engineering process ripe for automation, which saves both time and money for manufacturers.
As with most processes, we recommend approaching automation with a strategic lens. If you begin automating your data engineering process blindly, you can easily introduce technical debt in your system by choosing a data structure that doesn’t match the algorithm you need. Make sure you have a solid understanding of the problem to be solved before you begin the process of structuring data and constructing your data engineering pipeline. Work with key stakeholders not only to understand the problem but also their requirements.
Present Usable Output to the Right People
People often tout the power of machine learning, but neglect the delivery. For example, machine learning models typically output data in a .csv file. We’ve seen companies invest significant effort to generate insightful and actionable data — only to have that .csv file buried in a folder somewhere and left to collect dust.
Start your project by defining who needs to use the information generated by IoT remote monitoring sensors. Often, the intended recipient is in a unique environment; they may be operating machinery and not have access to email or even a traditional computer during their shift, for example. Consider how they will receive the information as you define the ideal output. What information do they need to see, and in what form do they need to see it? In some cases, automated email alerts may be most useful. In others, a reporting dashboard will best meet user needs, or perhaps PDF documentation. Make sure you understand the users and their needs well.
Putting These Principles Into Practice
Leveraging the data generated by your IoT remote monitoring systems is difficult to do without the right tools. That’s why we helped SUN Automation Group develop the Helios machine learning platform, a hardware and software edge computing solution that collects machine data to facilitate analysis and understanding of machine health. Clients who use Helios realize substantial improvements to predictive maintenance capabilities.