BLOG
How Remote Monitoring Benefits Manufacturing
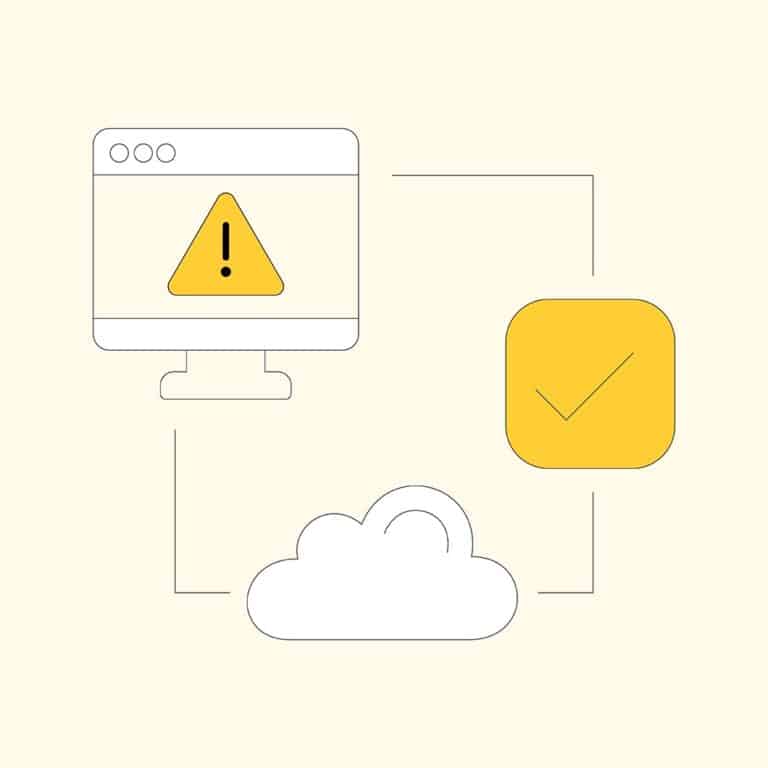
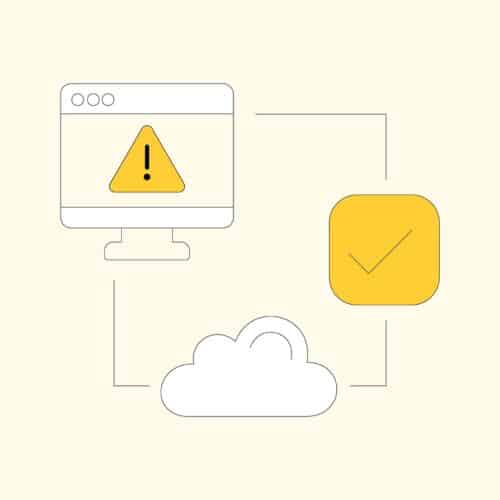
Remote monitoring is a key driver transforming the manufacturing industry. Not only does remote monitoring empower cost benefits, but it also creates efficiency standards that resonate from the factory floor to the customer’s door.
In this article, we’ll define remote monitoring, explain how it works, and provide examples of how manufacturers can leverage this technology to benefit their businesses.
What Is Remote Monitoring?
Remote monitoring is the process of collecting and analyzing machine health data from a distance. Typically, remote monitoring systems depend on IoT devices and AI-enabled reporting platforms.
How Remote Monitoring Works
Remote monitoring leverages a tech stack based on the Industrial Internet of Things (IIoT) and artificial intelligence (AI).
The process is pretty straightforward: IoT sensors monitor machine operation and productivity, then send that data to the AI platform for analysis. Personnel can access real-time data on machine function at any time. They also receive detailed reports that detail how their machines are performing over time.
The AI system makes predictions as to when a breakdown is likely to occur, reducing unnecessary downtime, maximizing machine uptime, and optimizing maintenance resources.
6 Key Benefits of Remote Monitoring for Manufacturing
Before remote monitoring, machines simply sounded an alarm as they were failing. Factory floor managers would be dispatched to assess the problem. Then, technicians would arrive to diagnose and troubleshoot, parts would be ordered, and the repair scheduled. In the meantime, employees would have to quickly find an alternative to maintain productivity – and that wasn’t always possible.
Today’s remote monitoring improves on this model, making the process more predictable and efficient. Here are some key benefits manufacturers gain with remote monitoring:
- Cost reduction
- Support for predictive maintenance programs
- Increased machine uptime
- Accurate predictions for machine or part failure
- Removal of the middleman
- Reduction in service calls
1. Remote Monitoring Reduces Costs
Remote monitoring reduces costs in many areas throughout an organization, but most notably in labor and maintenance.
Machines that are monitored remotely require fewer workers to keep operations running smoothly. Stakeholders also have complete visibility into production levels and machine efficiency, helping them make accurate real-time decisions.
2. Remote Monitoring Enables Predictive Maintenance
Over time, the AI system gathers enough data to predict at what intervals a machine or part is likely to fail. Remote monitoring helps companies recognize the events that precede a breakdown, enabling proactive repairs and maintenance to avoid costly downtime.
3. Remote Monitoring Maximizes Machine Uptime
Manufacturers waste a lot of money on unnecessary machine maintenance. While scheduled maintenance isn’t necessarily a bad thing, taking a machine offline while it’s still working well is not always the most efficient approach.
Coupled with predictive maintenance, remote monitoring helps manufacturers keep machines running at capacity.
4. Remote Monitoring Accurately Predicts Machine or Part Failure
When a machine breaks down, all resources are directed towards getting it fixed and back up to speed. Technicians diagnose the problem, parts are ordered, and production slows until the repairs are completed.
When a breakdown or slowdown can be triaged and diagnosed remotely, organizations enable end-to-end efficiencies and eliminate the need for multiple service calls and repairs.
5. Remote Monitoring Removes the Middle-Man
In many cases, remote monitoring eliminates the need for management or employee intervention entirely. When a failure is imminent, the monitoring system can communicate directly with service teams, ensuring an expedient repair or service process.
6. Remote Monitoring Reduces Service Calls
Remote monitoring can reduce the need for repair and service tasks by a significant margin. Personnel can identify and troubleshoot issues earlier, often resolving situations before they reach a breakdown state.
Going Remote: How Global Companies Stay Lean and Compliant, Even at a Distance
Given the size and scope of their facilities, large, global manufacturers often lack visibility into their daily processes. This presents a problem, especially in high-compliance industries like food products and energy, which are held to stringent safety, reliability, and viability standards.
Companies that run initiatives in remote locations are also challenged by added maintenance costs and lack of system visibility.
Remote monitoring solves this issue by supplying access to real-time alerts and data – enabling on-the-spot mitigation without missing a beat. When data is required to verify compliance, it’s readily and instantly available, minimizing production delays and ensuring work carries on as expected.
Case Study: Building an IoT Remote Monitoring Solution to Transform Data Into Insights
Saunders Electric has provided reliable portable power for live broadcasts and Hollywood productions since 1952. The company is a leader in innovative, energy-saving systems and serves as an alternative energy partner to Sandia National Laboratories.
Although Saunders had the technology to monitor equipment and power usage locally, they had no way to view the data differently or to monitor their systems remotely, limiting their capabilities – and their growth potential. They needed a way to modernize the way their systems ran without changing the core technology – something that would be easy to manage and give them more control.
Very teamed up with Saunders to develop a custom operational dashboard, unlocking data insights that allowed operators to proactively identify and address power usage issues. The team also set up data aggregation to a centrally managed cloud platform powered by Amazon Web Services.
The project benefits didn’t end there, however. Now that Saunders had access to all of their data in a central cloud server, they could access robust reporting tools to identify areas for optimization. Members of their sales team could also create dashboards to explain the return on investment to clients, a significant upgrade from the spreadsheets used prior.
Remote Monitoring-As-A-Service: Adding Value With Real-Time Data Visibility
Much like Saunders Electric, most industries will find tremendous value in remote monitoring. With real-time data at your fingertips, remote monitoring opens a world of possibilities and illuminates patterns that help businesses improve. These insights support improvements in areas that include customer service, machine operation, maintenance, and predictive analysis.
However, not every manufacturer has the bandwidth to manage and monitor all their systems efficiently. Most legacy systems operate on a closed network. There’s no impetus on organizations to take their systems online, given that it could expose them to security concerns and, possibly, an IT burden that’s not in their wheelhouse.
SaaS remote monitoring platform architecture addresses these issues. Systems are configured to circumvent the internal network and interface with machine IoT sensors, allowing companies to access the benefits of remote monitoring while still using their existing machines. This solution removes perceived barriers to modernization, providing access to next-generation efficiencies that help them compete with the disruptors in their space.
Machine manufacturers who add remote monitoring capabilities to their repertoire of services offer added value for their customers and create the potential for a new income stream based on that capability. With access to immediate and often touch-free maintenance, even small companies can make quick leaps and bounds in profitability. When their employees don’t have to worry about machine operation, maintenance, or efficiency optimization, they can focus on higher-level work, like building new business and delighting their existing customers.
Conclusion
Remote monitoring is essential in today’s competitive landscape. It optimizes machine function, extends uptime, and reduces losses from downtime, one of the biggest threats to profitability. With remote monitoring benefits, manufacturers are now able to do more with less, maximizing resources and setting new standards of machine efficiency.